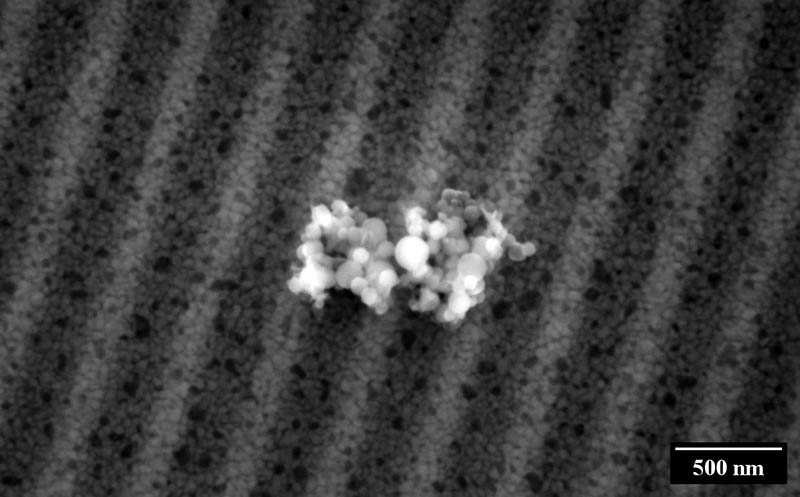
A Mizzou Engineering team has provided direct evidence of a localized explosion of an aluminum nanoparticle, a mechanism first theorized in 2006.
“This reaction mechanism has been proposed for over a decade but hasn’t been clearly observed experimentally until now,” said Matt Maschmann, associate professor of mechanical and aerospace engineering and co-director of the MU Materials Science & Engineering Institute.
Maschmann and Shubhra Gangopadhyay, professor of electrical engineering and computer science, outlined their observation of spallation of isolated aluminum nanoparticles by rapid heating in the journal of Applied Materials & Interfaces.
Aluminum nanoparticles are about 120 nanometers in diameter and are encapsulated with an aluminum oxide shell that protects the metallic aluminum core from reacting with the outside environment. When that shell is removed — in this case using lasers — and the core is exposed to oxygen, it releases a significant amount of energy. The key mechanism in this work was rapid (greater than 10,000,000 oC per second) thermomechanical expansion and melting of aluminum caused by focused laser heating.
“We’re the first to study this under the microscope, to initiate this reaction with fast heating,” Gangopadhyay said. “We did this in situ observation in a very controlled setting.”
In short, this nanoscopic explosion means researchers can control the release of a large amount of energy in a small, localized area. That energy could be used in applications such as biomedical imaging and treatment, material processing and energy storage.
“The energy contained in this material amounts to more than traditional explosives like TNT,” Gangopadhyay said. “There’s a lot of interest in this so-called nano thermite.”
Gangopadhyay has been studying nano processes for the last 25 years and has several patents around nanotechnologies related to converting high temperatures and pressures into energy. In 2014, Maschmann joined her team and began to apply mechanical engineering principles to her findings to further investigation of materials.
“The beauty of this now is that we can do it at the nanoscale, very localized level that was not done before,” she said. “There is a lot of potential, particularly for biological applications such as localized killing of cancer cells or genetic tissue modification.”
Because the aluminum nanoparticles are much smaller than biological cells, this process could create tiny shockwaves that would have effects even within a single cell, Maschmann said.
Another interesting application will be understanding what happens to materials under shock, Gangopadhyay said, pointing out that civil engineers — including Mizzou Engineering’s Hani Salim — have studied blast-resistant materials such as walls and glass at large scale.
“Here, we can put blast resistant materials in the lab and generate that kind of blast microscopically to see what effect it has on material properties on the micro and nanoscale,” she said.
Maschmann said one of the next steps is to determine whether the team can generate the same reaction on a larger scale.
“It’s not clear whether this would happen with bulk material,” he said. “We can do it with one particle, can we do it with many? It will be interesting to see how we can apply it to various settings.”
Co-authors of the paper were Naadaa Zakiyyan, a PhD student in electrical and computer engineering; Cherian Mathai, a research scientist at Mizzou Engineering; and Jacob McFarland, an associate professor of mechanical engineering at Texas A&M.