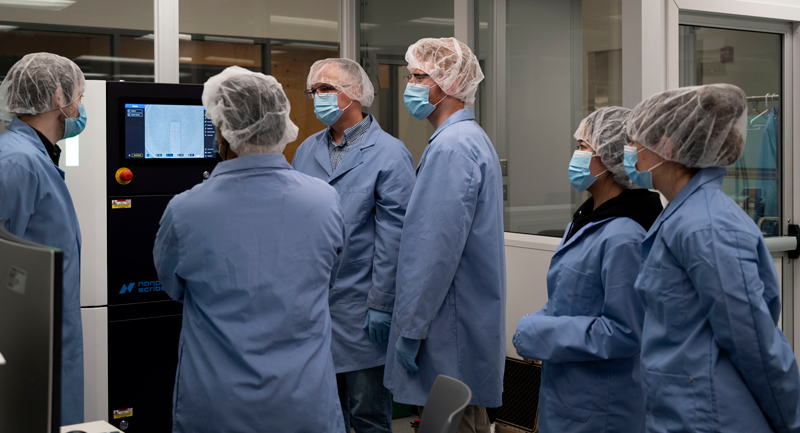
Researchers at Mizzou have spent eight years trying to figure out a way to fabricate a complex microfluidic filter that would allow doctors to efficiently recover cancer cells from patients blood without damaging the cells.
Now, they can easily make a prototype, thanks to a new Nanoscribe Quantum X Shape high-resolution 3D printer at Mizzou Engineering.
“We have been working to fabricate a new design since 2021, and this printer showed that it can accomplish that in 20 seconds during a demonstration,” said Elliott Leinauer, a Ph.D. student in electrical engineering.
Purchased with nearly $1 million from a U.S. Army Engineer Research and Development Center (ERDC) grant, the Quantum X Shape from Nanoscribe, a Bico company, uses a process called two-photon lithography to rapidly cure a liquid resin, making it ideal for rapid prototyping and wafer-scale processing of any 3D shape. It’s the fastest and most accurate 3D printer for high-end microfabrication tasks on the market.
Mizzou Engineering is one of just a few U.S. organizations to have the printer and one of fewer than 100 around the world.
“The significance of the Nanoscribe printer is that it can print at resolutions smaller than the fundamental length scale of many interesting engineering problems, including biological cells and even the wavelength of light,” said Matt Maschmann, associate professor of mechanical and aerospace engineering. “Simultaneously, it can fabricate patterns up to 3 inches in diameter, making it a very robust tool for many applications.”
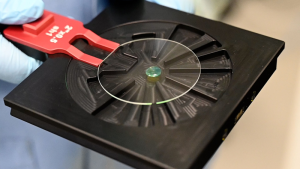
Those applications range from life sciences to microelectronics to advanced optics for security and defense, said Maschmann, who is also co-director of the MU Materials Science & Engineering Institute.
“This device is exciting for our research on new meta-materials for advanced optics that were designed by and for artificial intelligence,” said Professor Derek Anderson, principal investigator of the ERDC grant. “We have done much computationally and in simulation, and this device allows us to make prototypes to validate, compare and further our studies.”
For Leinauer, the printer is a game-changer.
—
Leinauer’s research focuses on finding a precise approach to let doctors extract live cancer cells from a simple blood draw.
That’s important because it opens up more customized methods to determine the best treatment. Right now, oncologists recommend chemotherapy, radiation and other cancer treatments based on what’s been successful in the past.
Being able to study a patient’s metastasizing cancer cells instead would allow doctors to test and recommend the best treatment based on that patient’s specific needs.
“Right now, when you try to extract cancer cells, they get damaged or die during the process,” Leinauer said. “We use a fabrication processes called photolithography to develop a filter that can capture the cancer cells. This fabrication process is the act of transferring micro/nano-scale geometric patterns from a photomask to a silicon wafer.”
The filter has a maze-like pattern that traps cancer cells, which are typically larger than most other cells. However, until now, there wasn’t a way to get them out of their filter without potential damage.
To alleviate that problem, Leinauer had the idea of making a design that could change shapes to release the captured cancer cells more easily without damaging them.
“The idea is that you use external loads to alter the geometry of the channels, converting this maze-like pattern into something more simplistic, which creates these fluidic highways for captured cells to escape the filter easily,” he said. “It’s a complex design, and fabrication was a significant barrier. This printer fixes that. It integrates photolithography fabrication principles with 3D printing of geometric designs at speeds and accuracy never before possible.”
—
Maschmann envisions using the Quantum X Shape for current research on semiconductor device patterning, as it can pattern circuits at the microlevel. The printer can also provide tiny geometrical designs that would allow him and collaborators to grow carbon nanotube films in specific patterns.
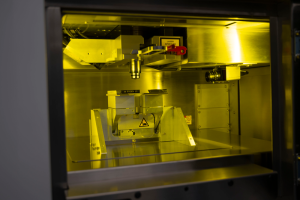
The technology may also be applied to advanced heat transfer applications. “It can manipulate liquid droplets for enhanced two-phase heat transfer,” Maschmann said. “When small droplets make contact, they release a lot of surface energy, energy so large that liquid hops off of a surface, which is great for heat transfer.”
Leinauer compared Quantum X shape’s technological advancement to going directly from the 30-ton computers of the 1940s to the latest smart phone.
“Mizzou is already a first-class research institution, but this sets us apart,” he said. “This is break-away technology. It allows us to pursue novel ideas that were simply unfeasible due to the limitations presented by traditional fabrication processes like photolithography. This printer completely changes what can be made and does so with relative ease, unshackling researchers from the bounds of yesterday’s fabrication capabilities to accelerate innovation.”
The printer, located on the third floor of Lafferre Hall, is available to researchers from across campus and to external users. Contact Joseph Mathai at mathaic@missouri.edu to learn more.